Mining equipment, fundamental to the mining industry, has evolved dramatically, impacting how resources are extracted and processed. This equipment ranges from simple hand tools to complex machinery, underpinning the industry’s productivity and efficiency. This blog post delves into the evolution of excavation equipment, the latest trends, and vital maintenance tips. It aims to provide a comprehensive overview, emphasizing the importance of these elements in enhancing operational efficiency, ensuring worker safety, and promoting environmental sustainability. Whether you’re a mining professional, student, or enthusiast, this post will offer valuable insights into the dynamic world of mining equipment.
The Evolution of Mining Equipment
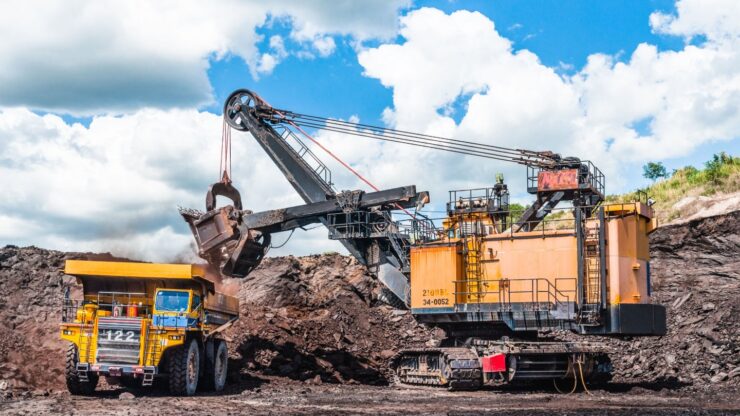
The history of mining equipment is a fascinating journey from primitive tools to advanced technology. In the early days, miners relied on manual labor, using rudimentary tools like pickaxes and shovels. The Industrial Revolution marked a significant turning point with the introduction of steam-powered machinery, which dramatically increased extraction rates and productivity. The 20th century brought further advancements with the advent of electrically powered equipment such as drills, excavators, and bulldozers, transforming mining operations. The late 20th and early 21st centuries have seen the rise of automation and robotics in excavation. These technological advancements, including automated drilling rigs and self-driving trucks, have not only enhanced efficiency but also reduced the risk of accidents, marking a significant leap in the industry’s evolution.
Current Trends in Mining Equipment
In recent years, the mining industry has embraced cutting-edge technologies, leading to revolutionary changes in equipment and operations. Automation stands out as a key trend, with an increasing number of excavation operations deploying remotely operated and autonomous machinery. This shift not only improves efficiency but also enhances safety by reducing human exposure to hazardous mining environments. Another significant trend is the integration of the Internet of Things (IoT) and data analytics in mining equipment. Sensors embedded in machinery collect real-time data, enabling predictive maintenance and operational optimization. This data-driven approach helps in identifying potential equipment failures before they occur, reducing downtime and maintenance costs. These technological advancements are reshaping excavation operations, making them more efficient, safe, and environmentally friendly.
Sustainability in Mining Equipment
The focus on sustainability in mining has grown exponentially, with a significant shift towards eco-friendly practices and equipment. Sustainable mining practices aim to minimize environmental impact while maximizing resource efficiency. This includes the use of energy-efficient machinery, which reduces greenhouse gas emissions and lowers energy costs. Additionally, there’s an increasing trend in using renewable energy sources like solar and wind power in excavation operations. The adoption of electric and hybrid vehicles in mining fleets is another example of this shift towards sustainability. These practices not only benefit the environment but also enhance the social and economic aspects of excavation operations, contributing to a more positive public perception and potentially reducing regulatory hurdles.
Safety Advancements
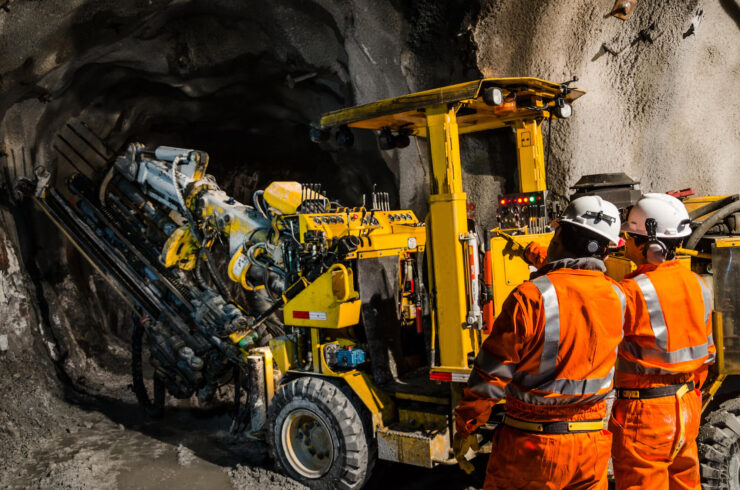
Improving safety in mining operations has always been a priority, and recent advancements in technology have made significant strides in this area. Modern excavation equipment is designed with enhanced safety features, such as improved ergonomics, automated systems that reduce human error, and protective structures to safeguard operators. Remote operation and automation technologies, as seen in Mammoth Equipment, have particularly been influential in enhancing safety by allowing miners to operate machinery from a distance, thus reducing exposure to hazardous conditions. These advancements demonstrate the industry’s commitment to protecting its most valuable asset – the workforce.
Maintenance Challenges in Mining
Maintaining mining equipment presents unique challenges due to the harsh working conditions and the complexity of the machinery involved. Equipment used in mining is often exposed to extreme weather, abrasive materials, and heavy loads, leading to increased wear and tear. This necessitates frequent maintenance and repairs to ensure operational efficiency and safety. The complexity of modern excavation machinery, with its integration of electronic systems and advanced technologies, requires specialized skills for maintenance and repair. Downtime for maintenance can be costly, both in terms of direct repair costs and lost productivity.
Importance of Regular Maintenance
Regular maintenance is critical for the longevity and efficiency of mining equipment. Proactive upkeep helps prevent unexpected equipment failures, which can lead to costly downtime and safety risks. A well-planned maintenance schedule ensures that equipment is in optimal condition, leading to better performance and longer life expectancy. Regular upkeep also provides an opportunity to upgrade equipment with the latest technologies, further enhancing efficiency and safety.
Maintenance Tips for Mining Equipment
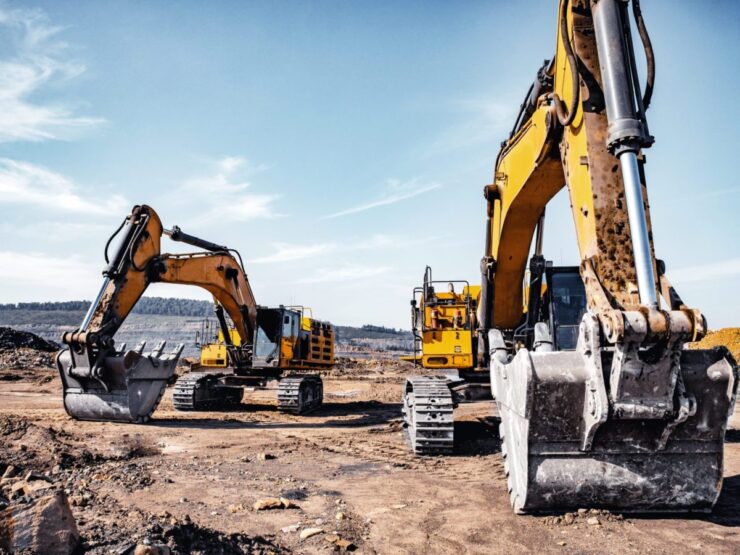
Effective maintenance of mining equipment requires a systematic approach. Key upkeep tips include regular inspection of machinery to identify wear and tear before it leads to major breakdowns. Lubrication is essential for the smooth operation of moving parts and should be done with the right type and amount of lubricant. Keeping equipment clean from dust and debris can prevent many mechanical and electrical problems. Prompt repairs are crucial; even minor issues, if left unaddressed, can lead to significant damages. Training maintenance personnel in the latest techniques and technologies is also vital for effective maintenance.
Training and Skill Development
The sophistication of modern mining equipment necessitates a skilled workforce for operation and maintenance. Training programs are essential to develop these skills, focusing on both technical and safety aspects. These programs should cover the latest advancements in excavation technology, equipment operation, upkeep techniques, and safety protocols. Skilled operators and maintenance personnel can significantly improve efficiency, reduce the risk of accidents, and ensure compliance with regulatory standards.
Cost-Efficient Maintenance Practices
Implementing cost-efficient maintenance practices is essential for maximizing profitability in the mining industry. Preventive upkeep, rather than reactive, is generally more cost-effective as it avoids the higher costs associated with equipment breakdowns. Outsourcing maintenance to specialized service providers can be a cost-effective strategy for some operations, leveraging their expertise and resources. Implementing energy-efficient technologies and practices can also lead to significant cost savings in the long run.
Case Studies
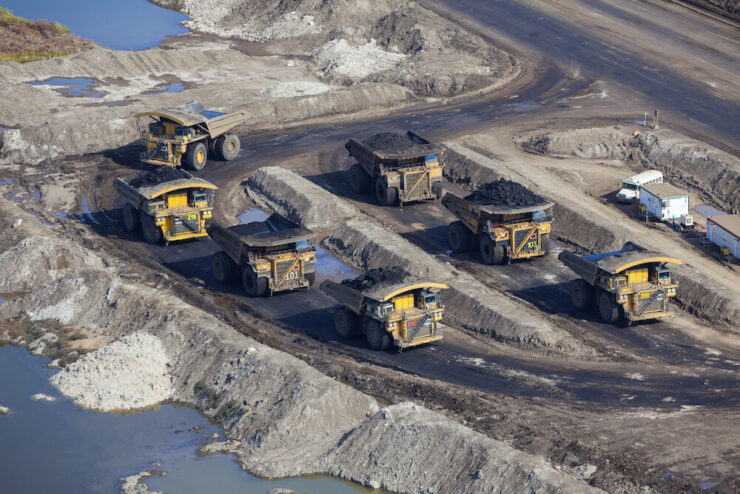
Real-world examples highlight the effectiveness of robust maintenance strategies in mining. For instance, an excavation company in Australia implemented a predictive maintenance program using IoT and data analytics, resulting in a significant reduction in unplanned downtime and upkeep costs. These cases demonstrate the tangible benefits of adopting advanced maintenance practices and technologies, offering valuable lessons for the industry.
Conclusion
In conclusion, the evolution of mining equipment, driven by technological advancements, has profoundly impacted the industry. Staying abreast of current trends and implementing effective upkeep strategies are crucial for long-term success. Regular maintenance, skilled workforce, and adoption of cost-efficient practices ensure the optimal performance of excavation equipment, enhancing safety, efficiency, and sustainability.