Sheet metal fabrication involves multiple techniques to create durable and functional metal parts, but the key to perfecting any project is the final surface treatment. Without the right approach, flaws can affect both the appearance and performance of the metal. The good news is that achieving a flawless finish is possible with the right methods and expertise.
Key Points
- Proper preparation is crucial before finishing.
- Surface quality determines both performance and aesthetics.
- Using appropriate tools ensures a uniform finish.
- Different types of finishes suit different applications.
- Patience and precision lead to the best results.
Preparation for a Flawless Finish
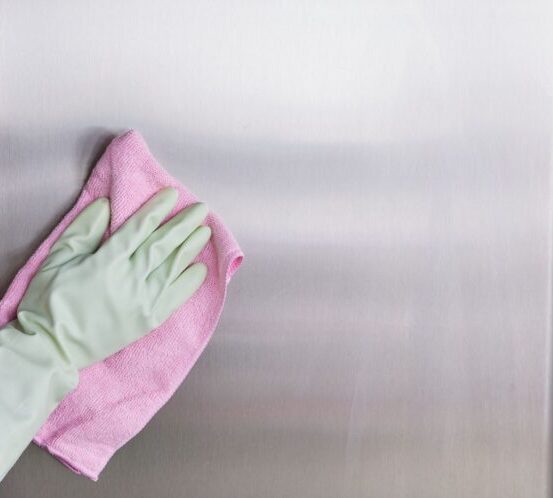
The foundation of a perfect finish starts long before the actual surface treatment begins. Different types of metal finishes are used in different situations and depending the requirements. Any impurities, scratches, or irregularities in the metal surface need to be addressed before applying any coating or polish.
Begin by thoroughly cleaning the metal to remove oil, dirt, or debris. Use a mild detergent and water, then dry the surface with a clean cloth. This step is often overlooked but is essential to prevent contamination, which can lead to an uneven finish.
Next, inspect the surface for imperfections. Even small dents or scratches can become more visible after finishing. Use fine sandpaper or a file to smooth out any uneven spots. For stubborn imperfections, a more abrasive tool may be required.
Tools for Achieving Precision
To achieve the best finish, the right tools are of the most importance. Handheld grinders, sanders, and polishing wheels are commonly used to smooth out the surface. Each tool serves a specific purpose, whether it’s removing material, creating a uniform texture, or polishing to a mirror-like shine. Be mindful of the pressure applied when using these tools. Too much pressure can cause overheating, which leads to warping or discoloration.
For a uniform finish, consider using a machine that can maintain consistent contact with the surface. This reduces the risk of unevenness. Hand finishing can also be effective, especially for intricate parts where machinery may not reach. Additionally, it can be important to ensure that the surface is free of contaminants or old coatings to achieve a precise finish. This is where abrasives for blasting can be used, where a high pressure system propels abrasive materials against surfaces. It can be especially useful for preparing large or heavily soiled surfaces before applying a new finish.
Types of Metal Finishes
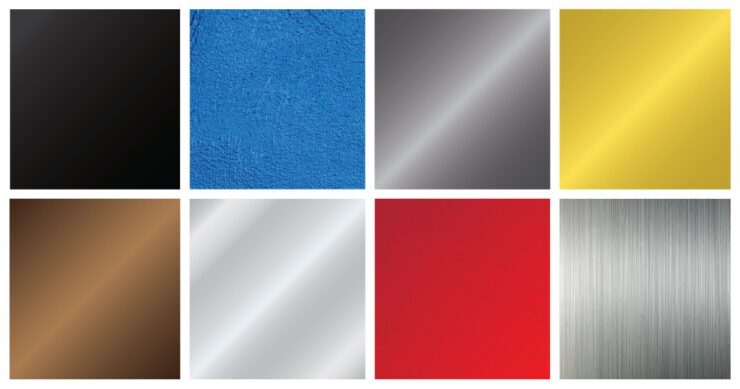
Finishing options vary depending on the desired outcome, such as durability, resistance to corrosion, or aesthetic appeal. Different finishes can enhance the surface in unique ways.
Some finishes offer excellent protection against corrosion and others are more about aesthetics, creating a sleek and modern look. It’s important to match the finish to the application to avoid compromising the part’s performance. Let’s see what option we have:
- Anodizing: Offers superior corrosion resistance and durability, often used for aluminum parts.
- Brushed Finish: Creates a smooth, textured surface for aesthetic appeal, commonly found in appliances and decorative pieces.
- Powder Coating: Provides a durable, protective layer that resists chipping, fading, and corrosion, suitable for outdoor applications.
- Polishing: Produces a mirror-like, shiny surface, often used for decorative or reflective purposes.
- Electroplating: Applies a thin layer of metal, like chrome or nickel, to enhance corrosion resistance and improve the appearance of the metal.
- Satin Finish: Offers a low-gloss, matte appearance, ideal for reducing glare while maintaining a clean, industrial look.
- Galvanizing: Coats the surface with zinc to prevent rust, commonly used for steel in outdoor environments.
- Sandblasting: Creates a rough, textured surface, often used to prepare the metal for painting or other treatments.
- Chemical Conversion Coating: Protects against corrosion by creating a non-reflective surface, often used in aerospace and automotive industries.
- Black Oxide Coating: Provides a dark, matte finish with mild corrosion resistance, commonly used in firearms and tools.
- Passivation: Enhances corrosion resistance, especially for stainless steel, by removing contaminants from the surface.
For those interested in exploring the variety of options, check out this detailed guide on types of metal finishes. The choice of finish should align with the specific requirements of the part and its intended environment.
Techniques for Applying Finishes
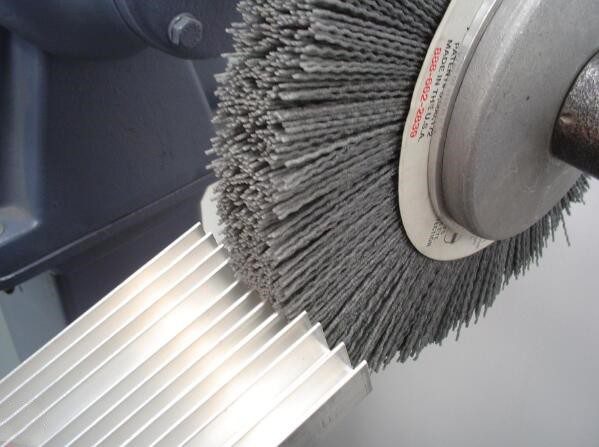
Several techniques are available for finishing metal, each with its benefits and limitations. Some common methods include:
Polishing: Ideal for parts requiring a smooth and shiny surface, such as decorative elements. Begin with a coarse abrasive and gradually move to finer grades until the desired smoothness is achieved.
Brushing: Provides a textured, satin finish, often used in applications where glare reduction or a clean industrial appearance is desired. A wire brush or abrasive belt is used to create parallel lines across the surface.
Powder Coating: An excellent choice for parts that need both aesthetic appeal and protection from harsh environments. The powder is electrostatically applied and then cured under heat, resulting in a durable coating that resists corrosion, chipping, and fading.
Anodizing: A process mainly used on aluminum, where the surface is electrochemically treated to increase corrosion resistance and wear durability. Anodizing also allows for coloring, making it a popular option for both functional and decorative finishes.
Electroplating: A process that involves applying a thin metal coating onto the surface using an electric current. This is often used to provide additional protection against corrosion or to improve the conductivity of the metal part.
Achieving Consistency Across the Surface
Irregularities, such as streaks or color variation, can undermine the quality of the final product. To avoid this, use controlled and uniform pressure during the finishing process. For example, when polishing, move in straight lines, rather than circular motions, to avoid uneven patches. If using machinery, set it to a consistent speed to prevent variations in texture or shine.
Another important factor is the temperature of the metal. Excessive heat from tools can affect the finish, causing discoloration or even altering the metal’s structural integrity. To prevent overheating, take frequent breaks and avoid applying too much pressure.
Post-Finishing Inspection
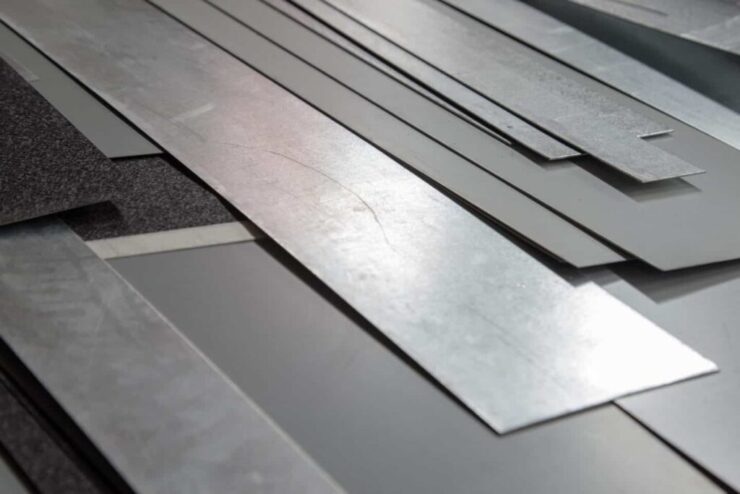
Once the finishing process is complete, inspect the surface for any flaws. Use a magnifying glass or a bright light to catch any minor imperfections that may have gone unnoticed. If necessary, perform touch-ups by gently reworking problem areas with fine abrasives. The goal is to achieve a uniform surface free from blemishes or irregularities.
Lastly, consider applying a protective sealant, especially if the metal will be exposed to harsh environments. A sealant can help preserve the finish and provide additional resistance to corrosion or wear.
FAQs
1. Why is it important to clean metal before finishing?
Cleaning removes contaminants that could interfere with the finish, ensuring a smoother and more durable surface.
2. What is the best tool for achieving a polished finish?
A polishing wheel or buffer is ideal for achieving a high-gloss finish on metal surfaces.
3. How can I prevent overheating during finishing?
Apply moderate pressure and take regular breaks to allow the surface to cool down. This prevents warping and discoloration.
4. What type of finish is best for outdoor applications?
Powder coating or anodizing provides excellent protection against environmental factors, making them ideal for outdoor parts.
5.How do I know which finish to choose for my project?
Consider the environment, aesthetic preferences, and functional requirements of the part when selecting a finish.
Conclusion
Achieving a flawless finish on metal requires attention to detail, the right tools, and patience. The process begins with thorough surface preparation and continues through careful application of the chosen technique. Consistency in pressure and temperature ensures a uniform result, and post-finishing inspection guarantees a high-quality surface.
For those seeking specific finish types or looking for guidance on what works best for their project, exploring the options available is essential. Ultimately, the finish should meet both aesthetic and functional needs, ensuring the metal part performs at its best.