Warehousing is one of the most important enablers of an efficient global supply chain network. You need to have a proper warehouse system and ensure that you get on the best warehouse for your business. Various dimensions of the supply chain, such as flexibility, shorter lead times, and corporate profitability, can be easily achieved through warehousing. There are different other advantages of warehousing, for instance, preservation and protection of goods. Other than that, the warehouse plays a major role in ensuring profits for a business.
The optimal warehouse location ensures the success of supply chains in terms of lower costs and higher profits, so yes, buying the warehouse is the right move to ensure success. Here you will get information about some of the necessary factors to evaluate warehouse ownership.
Some Of The Essential Factors To Consider While Buying The Warehouse:
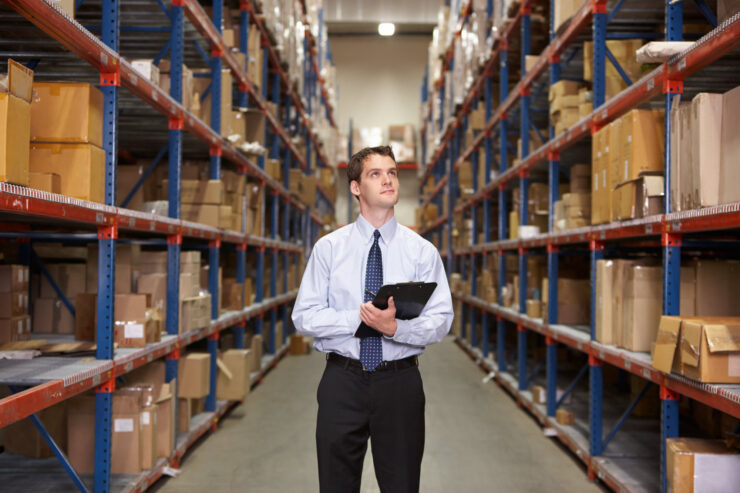
If you plan to get a warehouse somewhere near Houston, you must check several factors to ensure you can use the space best. You can maintain the supply chain no matter what the condition is. If you need houston warehouse for rent specialists, you can find here more information. Further, this article will discuss the essential factors to consider while buying the warehouse.
Storage Room:
If the company has strict storage and firefighting requirements for hazardous or flammable materials or even food items, it must ensure that the warehouse should fulfil the company’s needs. It should have all the necessary facilities for a business to grow. One of the most important things to consider is the storage space. If there will not be sufficient space, then how will you be able to store the stock?
Even when looking at the storage, many things need to be considered because different products need different environments. As an e-commerce order fulfilment or logistics tech company, you must understand how to handle products that require a chemical system versus a water-based system. These businesses should also consider the environment and should be aware of any nearby streams or bodies of water. If there are flammable products, then a proper storage facility should be there to ensure that there are no fire accidents.
Find The Right Location:
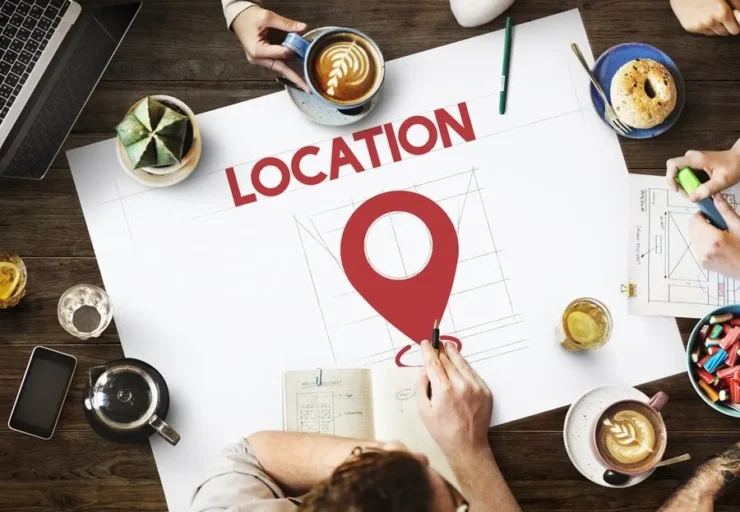
When choosing a warehouse, it is critical to consider the current shipping locations of the company’s suppliers as well as the delivery locations that will be arranged for customers. You have to check the convenience of the customers and, at the same time, the business operations. Warehousing close to your customers reduces unexpected logistical costs.
You don’t have to get any transportation that will increase the unnecessary cost. A convenient location can reduce transportation costs and travel time. It is also advantageous if your chosen warehouse is located near major transportation systems such as railways and shipping ports, as it will be easier for you to load the stock and easily access all the business operations. The location should also be favourable to the environment that you need for your stock or products.
Expected Risk:
Risks are some of the major things that need to be considered and known before taking any warehouse. Using an outsourced vendor for warehousing can eliminate many of the risks associated with logistics. The majority of this burden will be borne by the company partners, who will assist in resolving potential issues and working proactively to reduce the traditional problems associated with moving products with heavy machinery. You need to find the right sources that can assure you that there will be negligible risk involved.
Nonetheless, the company’s role must be active while mitigating risk by inquiring about incident rates, safety plans, insurance coverage, and damage plans from warehouse owners. When you take their services, they will guide you through the different things involved and, if something happens, then how it has to be tackled. Always request copies of insurance coverage, make specific plans and report incidents to match the company’s expectations.
The Availability Of Skilled Workers:
Obtaining a building in a remote location will obviously come at a low cost, but finding trained workers in such a location will be difficult and extremely difficult. When you set up a workplace, you need a workforce to lower the workload of your business operations. On the other hand, relocating your entire workforce to a remote location will be relatively inexpensive. You can’t easily do that, and it will increase the cost, which might not be feasible for you. Instead, you can show smartness and find the warehouse where you can easily get the workers.
The organization can only succeed in a sustainable manner if you have to pool the workers. As a result, it is best to locate your warehouse in an area that can provide you with an adequate workforce with a variety of skills. This will assist you in hiring employees for a variety of activities related to your organization. You can then plan out your operations accordingly.
Rent And Taxation:
When it comes to selecting an accurate location for the organization’s warehouse, the cost must be a critical criterion. Other than the major factors, cost ensures whether you are getting the right deal or not. There is a hidden cost that has a negative impact on the low lease rates, so cost factors should always be considered in any aspect of the business.
You need to be wise and check out different sources and also know why they are costing you that much and what all things are covered in that particular cost. Rental rates in some countries are measured in square feet per month or year, depending on the property owner’s needs. There are other criteria as well, so it is important to be aware of each and everything.
Bottom Line
Owing the right warehouse is important if you want to grow fast and ensure that your supply chain should not become slow. All these factors are really important to consider so that after the purchase you don’t feel any sort of regret and get the best outcome of your purchase.